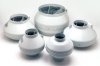
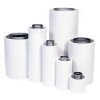
Ventilating your growing area
Correctly ventilating your growing area is a vital part of greenhouse/grow room design. Adequate ventilation in the grow room is important for a number of reasons – temperature, humidity, disease and odor control, and fresh/stale air exchange. The calculations that are used to correctly design a ventilation system can be quite complex and require numerous known variables. The purpose of this article is to simplify these calculations while helping you to better understand grow room ventilation.
How to size your exhaust fan
There are many calculations on the web for sizing a fan for ventilating grow rooms; however, what these calculations fail to take into consideration is the friction loss on carbon filters, increased temperatures from HID lights and CO2, etc. The following calculation can be used as a guide for sizing an exhaust fan for a growing area (keep in mind that this calculation will give you the lowest required CFM required to ventilate the grow room):
Step 1 – Room Volume
First the volume of the room needs to be calculated. To calculate multiply length x width x height of growing area e.g. A room that is 8' x 8' x 8' will have a volume of 512 cubic feet.
Step 2 – CFM Required
The fan should be able to adequately exchange the air in a grow room once every three minutes. Therefore, 512 cubic feet/3 minutes = 171 cfm. This will be the absolute minimum cfm for exchanging the air in a grow room.
Step 3 – Additional factors
Unfortunately, the minimum cfm needed to ventilate a grow room is never quite that simple. Once the grower has calculated the minimum cfm required for their grow room the following additional factors need to be considered:
- Number of HID lights – add 5% per air cooled light or 10-15% per non-air cooled light.
- CO2 – add 5% for rooms with CO2 enrichment
- Filters – if a carbon filter is to be used with the exhaust system then add 20%
- Ambient temperature – for hot climates (such as Southern California) add 25%, for hot and humid climates (such as Florida) add up to 40%.
In our 8’ x 8’ room we have 2 x 1000w air cooled lights, and we plan to use a carbon filter. We also plan to use CO2 in this room. The ambient temperature is 90°F, however, we will be using air from another room that is air-conditioned.
Minimum Required CFM to ventilate room:
(CFM required for room – step 2) + (CFM required for room – step 2 x 10% (2 air cooled lights)) + (CFM required for room – step 2 x 5% (CO2)) + (CFM required for room – step 2 x 20% (Carbon Filter)) + (Ambient Temperature 0 (Air coming from air-conditioned room)).
= (171cfm) + (171cfm x 10%) +
(171cfm x 5%) + (171cfm x 20%) + ( 0 )
= 231cfm – this is the absolute minimum cfm required to ventilate your room.
The next step would be to match the closest fan to this CFM. As we are using a carbon filter we will need to match the fan with the filter so that the fan that will neatly fit onto the filter. The filter that we will use is a Dutch Breeze Carbon Filter - DFS4. The DFS4 has a 6" flange. Our options for 6" fans are as follows:
- Eco Plus 6” – 440cfm
- Fantech 6” – 252cfm
- Fantech 6” XL – 392cfm
- Elicient 150B – 309cfm
The DFS4 filter has a cfm rating of 255-309, so the fan that we will choose for our room will be the Elicient 6” fan. This will be an ideal fan for this room and carbon filter, since the extra cfm will help compensate for the small amount of ducting we may have to run.
If only step one and two was used (the calculation that is most commonly displayed on garden websites) then the grower would have chosen a 4” fan and a 4” carbon filter; the grower would have soon found out that this fan and carbon filter would have been inadequate for their grow room.
Example 2:
If all the variables are kept the same and we changed the room size from 8’ x 8’ to a 12’ x 12’ then the minimum required CFM would be 519 cfm, thus the fan would be Fantech 8” XL, Elicient 8” or EcoPlus 8” and the DFS5 or DFS6 Dutch Breeze carbon filter.
The Really Simple Method:
If you want to keep things really simple, just remember that you want to replace the air in your grow room every one to three minutes. If you're in a hot area, exchange it every minute; if you're in a cooler area, you can take up to three minutes.
The Very Important and Often Overlooked Intake Port
It is very important to understand that you can't simply put an exhaust fan in a sealed room and expect to suck air out of it. You absolutely must have some kind of opening in the room to allow fresh air to replace the air you are exhausting. If you don't understand this concept, just put your finger over one end of a straw and try sucking out of the other end - you'll find that the walls of the straw collapse inward and that you can't suck any air out. If you were to poke a small hole somewhere in the straw, you will find that you can now suck air through it; the bigger the hole, the more air you can suck. Obviously, any fan you install in your grow room isn't going to be powerful enough to create enough negative pressure to suck the walls inward, but what will happen is that your fan will draw more energy, make more noise, run hotter, break down much sooner than it should, and finally, suck very little (if any) air out of the room. An intake port can be anything from a gap under the door to an open window - even a hole in the wall. The best place for an intake port is diagonally opposite from your exhaust fan; that way, air has to pass across the entire room - very efficient. You can put a piece of screen over the opening to keep insects and animals out, a piece of A/C filter to keep dust out, or a Louvered Shutter or Backdraft Damper that opens when the fan turns on and closes when it turns off. You can also use a Motorized Damper. This gets installed in-line with your ducting and is plugged into whatever device controls your exhaust fan. When your fan turns on, it allows air to pass. When your fan shuts off, it seals completely, preventing CO2, air, odor, etc. from passing. You can get creative with these devices and use one fan to control two rooms, etc.
One last note about intake ports - you will see much better results from your exhaust system if you install a second fan to create an active (as opposed to passive) intake system. Normally, when your exhaust fan sucks air out of your room, air is passively going to get sucked back into the room. By installing a second fan on the intake side, you will reduce the amount of negative pressure created in the grow room, thereby cutting down greatly on the amount of work the exhaust fan has to do and allowing much more air to pass. Ideally, the intake fan should be the same size as the exhaust fan, but it can be a little smaller if necessary. If you're not sure or you don't want to spend the money, start out with just an exhaust fan. If it's not performing as well as you thought it would, try adding an intake fan - you'll smile when you see the difference!
Fan and Carbon Filter Placement
If no carbon filter is being used then place the fan at the highest possible point in the room; the reason for this that hot air rises and it is the hot air that needs to be exhausted. Also, place the fan on the opposite side of your intake. The negative pressure that the fan creates in the room will pull air from the intake opening across the garden and towards the fan. This will bring the fresh air over the plants while displacing the old stale air.
If a carbon filter is being used then place the fan on top of the filter. There are two options that a grower can use with the carbon filter: 1) Suck through the filter or 2) Blow through the filter.
Sucking air through filter is the preferred method. Carbon filters should be placed on the floor standing upright or hung horizontally from the ceiling. Place the fan and filter in the room opposite the intake port. From the fan, attach ducting so as to exhaust the scrubbed air out the room. Keep the ducting as short as possible and avoid any bends in the ducting. Keeping the ducting as short and as straight as possible will reduce the friction loss and noise.
Blowing through the filter is a less commonly used method of exhausting. The benefit is that the fan can be placed at the highest point in the room and the hot air is sucked out of the room and forced through the filter. However, if you're using the fan/filter combination as part of your exhaust system (as opposed to just an odor scrubber), it will need to be placed outside of the growing area.
Before using a carbon filter for the first time always take the filter outside and then first suck, then blow through it before installing it in your growing area. This will blow out any carbon dust which is created in the filter during transport. During normal operation always keep the dust sock on the filter; this stops large dust particles from blocking the filter and will help prolong the life of the filter.
Air Circulation
Always provide your plants with adequate air movement and circulation in the grow room. Air circulation within the room eliminates stale spots and also reduces the formation of micro-climates within the leaf canopy. If air circulation in the grow room is poor then the micro-climate in between the plants increases in humidity and temperature. This can result in mildew and insect problems, as well as less deficiencies. For adequate air circulation use a wall mounted fan; 2-3 fans will provide sufficient air movement. Never switch these fans off unless you are spraying or fogging your room.
.
Air Cooled Reflectors
Air-cooled lighting involves the use of inline fans and ducting to extract heat away from the lamp and out of the growing area. All air-cooled reflectors sold by BGH can be sealed with a tempered glass lens, isolating the heat of the lamp from the cooler environment of the grow room. The main purpose of utilizing an air cooling system for HID lights is to efficiently extract the heat produced by the bulb before it has a chance to pass into the growing area.
Air-cooling offers several benefits to the indoor gardener:
- Reduces or eliminates (especially in summertime) heat problems - lamps are the primary source of unwanted heat. A properly air cooled light can remove up to 50% of the heat of the lamp.
- Gives greater control over temperature and humidity in the plants’ growing environment, allowing for optimum growth rate management and the development of healthier plants and higher yields.
- Allows HID lights to be placed closer to the plants, increasing the intensity of the light they receive, thus resulting in faster growth rates and larger yields.
- Reduces the cost of running a large air-conditioner in the growing room.
- Most growers use vent fans to replace hot air in the grow room with cooler air from the outside, but this practice can quickly deplete CO2 tanks when supplemental CO2 is being used. By air cooling the lights, you can reduce the temperature of the grow room enough so that you don't need an exhaust fan, or at the very least, get away with a small air conditioner.
- Helps keep the bulb cooler, resulting in less bulb stress and failures.
- It is much easier to remove heat at the source rather than try to get it after it has entered the grow room. Due to the small volume of air in the reflector (compared with the entire volume of the grow room), much less energy and effort is required to remove the same amount of heat.
There are many methods to cooling HID lights. Here are a few:
Type 1 - Inline Series (without CO2)
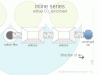
There are many variations of this type of setup. In this setup, the system used to air cool the lights is also used to ventilate and clean the air being exhausted from the grow room. This system effectively uses one fan to do the job of two fans. The fan will need to be sized larger than what is required to just ventilate the room. The fan will need to pull air through a carbon filter, through one or more lights and exhaust the hot air. This system is suited for small to medium growing areas without the use of CO2. The fan should be running continuously during the light period (which means it is possible to plug the fan into the same timer that is used to operate the lights [provided they both don't exceed the amperage rating of the timer]). Ideally, the fan should stay on a little longer, since it takes a while for the bulb, reflector, ducting, etc. to cool down completely (which means you would have to use a second timer).
Materials required:
- Air Cooled Reflectors
- Ducting to match reflector and fan - 4", 6", 8"
- Duct Clamps - 4", 6", 8"
- Centrifugal Fan
- Carbon Filter
- Timer for Fan
- Grow Yoyos
Type 2 - Inline Series (with CO2)
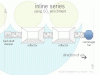
This type of cooling system pulls air (preferably from a cool air source) through the lights and exhausts it outside or into another area. The air passing through the light never comes in contact with CO2-rich air in the grow room. This allows the grower to control CO2, temperature, humidity and also groom ventilation. This also allows the grower to create a sealed environment. This type of setup is suited to small to medium sized areas. If 2 x 400w lights are being used in a grow room, then a 4" or 6" fan could be used to cool the lights. If the air that is being used to cool the lights is warm/hot, then a 6" fan should be used; if the air is cool then a 4" fan can be used. Use 6" ducting to connect the fan to the reflectors. With the addition of a 6" ZoneMaster Motorized Damper on the intake side, you will get the added benefit of keeping moisture and dust from entering the system at night, which could cause condensation and alter the temperature and humidity levels in the grow room as well. The Zone Control Damper should be plugged into the same timer as the fan. When the lights turn on and the fan is activated to cool the lights, the Zone Control Damper is also activated, thus allowing cooler intake air to cool the lighting system. Alternatively, you could install a 6" Suncourt inline booster fan on the intake side in place of the damper. When the lights turn on and the fan is activated to cool the lights the booster fan is also activated, creating positive pressure in the air cooling system and increasing the air flow and efficiency of the system. This is especially useful if you decide to add another light in the future or you find that the single fan system isn't moving enough air (which is a common problem when you use too much ducting or too many sharp bends in the duct run).
Materials required:
- Air Cooled Reflectors
- Ducting to match reflector and fan - 4", 6", 8"
- Duct Clamps - 4", 6", 8"
- Centrifugal Fan
- ZoneMaster Motorized Damper
- Suncourt Fan
- Timer for Fan
- Grow Yoyos
Type 3 - Parallel Series (Without CO2)
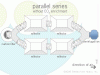
This type of system is similar to Type 1 above, however this configuration is more suitable for larger growing areas. This system utilizes only one fan to cool numerous lights. It is more efficient to cool lights this way instead of using one fan to pull air through numerous reflectors in one line. It's not efficient to pull hot air from one reflector into another (which is also producing heat) into another (even more heat) and into another (yet more heat). This will cause too much heat to radiate from the hot reflectors into the grow room. It also puts a tremendous strain on the fan when you go from a 10" or 12" fan into a long run of 4" or 6" ducting. This strain will shorten the life of the fan and use more energy. By using "Y" Adapters you can can go from a 10" or 12" fan into two 6" or 8" runs - a much more efficient solution to the problem. You can either leave the intake ends on the last two reflectors open, or (as illustrated below) you can add another "Y" Adapter, ducting and a carbon filter to clean the air before it comes in contact with the system. Not only does this prevent any odor from exiting the room, it also keeps dust from entering the lighting system, which could accumulate on the glass lens and reduce the amount of light available to the plants.
Materials required:
- Air Cooled Reflectors
- Ducting to match reflector and fan - 4", 6", 8"
- Y Adapters - various sizes
- Duct Clamps - 4", 6", 8"
- Centrifugal Fan
- Carbon Filter
- Timer for Fan
- Grow Yoyos
Type 4 - Parallel Series (With CO2)
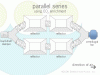
This is by far the most popular setup for air cooled lights that are utilizing supplemental CO2 in the growing area. As with the Type 2 system above, air is pulled from another area to cool the lights. With the inclusion of a "Y" adapter the grower can air cool numerous lights with only one fan. If 4 x 1000w lights are being used in a grow room then an 8" or larger fan should be used to cool the lights. Use an 8" x 6" x 6" "Y" Adapter to run from the fan to the reflectors. BGH offers several different sizes of "Y" Adapters and Duct Reducers allowing you to use just about any size fan with any size ducting. The same setup can be used on the intake side with the addition of an 8" ZoneMaster Motorized Damper or 8" Suncourt Inline Booster Fan (as explained in Type 2, above). The Zone Control or Suncourt fan should be plugged in with the same timer as the fan. When the lights turn on and the fan is activated to cool the lights, the Zone Control or booster fan is also activated, thus allowing cooler intake air to cool the lighting system.
Materials required:
- Air Cooled Reflectors
- Ducting to match reflector and fan - 4", 6", 8"
- Y Adapters - various sizes
- Duct Clamps - 4", 6", 8"
- Fan
- Carbon Filter
- ZoneMaster Motorized Damper
- Timer for Fan
- Grow Yoyos
any other bits wanting to include please do